Alignment and assembly of LiDAR systems
When accuracy is crucial in the production of LiDAR systems in high volumes
Light Detection and Ranging (LiDAR) is established on the market as a technology for realizing autonomous driving. Within the next two years, more than 20 vehicle models with at least one integrated LiDAR are expected to be launched on the market. The goal will be to achieve automated driving on highways, which is the first step toward reaching Level 3. The major task remains to make the systems as safe, robust and reliable as possible. TRIOPTICS supports as a partner in the development of a production process for high-volume production of automotive LiDAR systems.
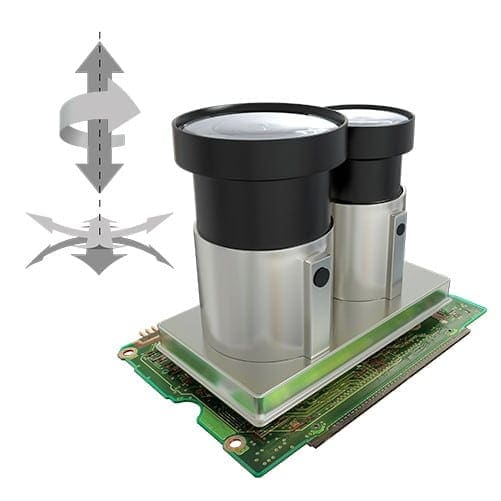
Precise alignment for maximum performance
No matter what you call them, scanning or non-scanning, mechanical or non-mechanical, Flash LiDAR, Solid-state LiDAR or MEMS-LiDAR – all LiDAR systems have one thing in common: The interaction of the optics and sensor chip of the emitter and receiver unit of the LiDAR sensor must be absolutely precise and perfectly aligned. If the components are not precisely positioned, objects and distances cannot be reliably detected. In the worst case, this could impair the safety of autonomous vehicles. Accordingly, perfect performance must be ensured from the first sample to the series product.
Depending on the type of LiDAR, active or passive alignment for high-precision positioning can be considered to analyze and control image focusing.
Systems for maximum output and production speed
Our equipment achieves maximum yield and production speed to enable a production of over a million sensors per year. A fully automated production line with pre-testing of components, a sensor-specific alignment process for optical elements and end-of-line (EOL) testing for the final product. The entire system meets the requirements of the automotive industry for highest OEE (Overall Equipment Effectiveness) in terms of 24/7 production with maximum availability as well as traceability of production data and connectivity to MES systems.
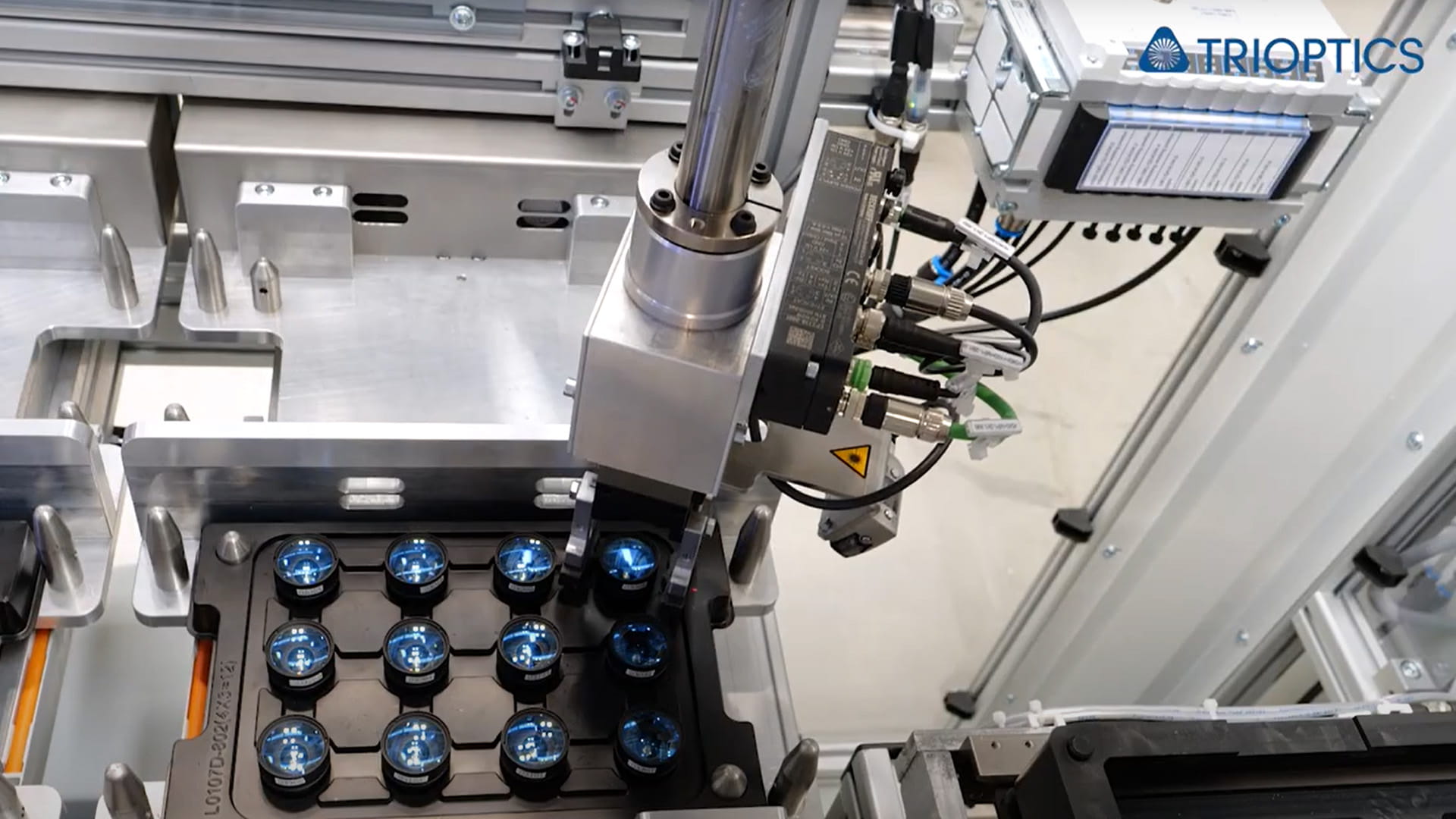
LiDAR alignment methods
How to choose the best optical assembly method depending on the LiDAR type?TRIOPTICS classifies the alignment of LiDAR components into two different methods: active and passive alignment. Which is the best method depends on the customer-specific LiDAR system.
Active Alignment of LiDAR systems
Active Alignment of LiDAR works in a similar way to Active Alignment of cameras. Typical features of the Active Alignment method for LiDAR:
- The laser is activated and/or the receiver is switched on for image acquisition
- The alignment is done by detecting the laser beam pattern or by image processing of the receiver signal
Passive Alignment of LiDAR systems
The term refers to a process that uses inactive (passive) components of the LiDAR sensor. Typical features of the Passive Alignment method for LiDAR:
- The Laser and/or the receiver are not powered up
- The alignment is done using visible structures or special markings as reference