MOTOR-CONTROLLED: OptiCentric®101 increases precision
Motor-controlled positioning of additional measuring sensors on OptiCentric® 101 increases precision
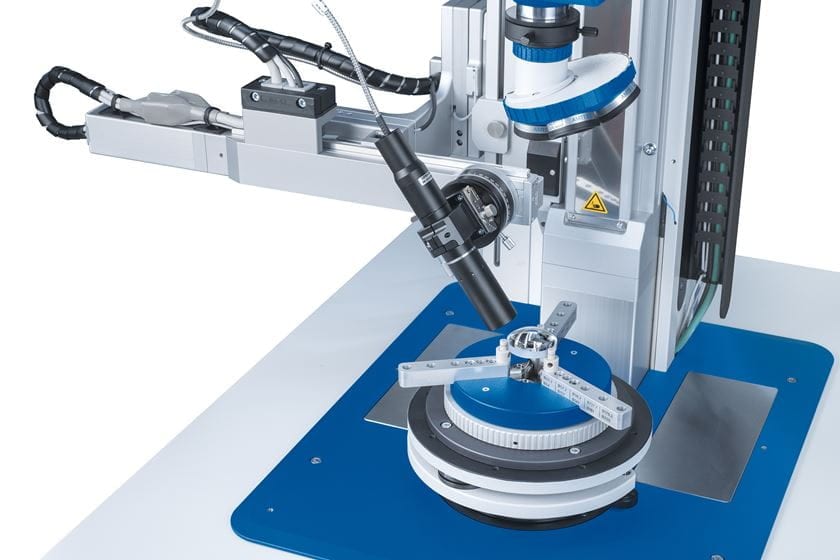
At LASER World of PHOTONICS 2022 in Munich, TRIOPTICS presented its worldwide as standard recognized centration measurement system OptiCentric® 101 Dual in combination with the new motor-controlled tool stage for additional measurement sensors. Adding measurement sensors to the basic unit is particularly advantageous for the measurement of aspheres as well as for non-contact lens edge and barrel determination. Motorization not only guarantees higher measuring accuracy compared to manual processes, but also enables faster changeover as well as increased process reliability.
Asphere measurement with AspheroCheck®
The alignment of the aspherical lens surface in regard to the paraxial optical axis is an important quality criterion for aspherical lenses – both axes must coincide. A corresponding check of the individual elements can be performed with the OptiCentric® AspheroCheck®: While an autocollimator measures the centering of the paraxial optical axis during a sample rotation, a distance sensor measures the run-out at an off-axis zone of the aspherical surface. In this way, precise information about the orientation of the aspherical surface is obtained.
Centration measurement in regard to the lens edge and barrel
Many applications require that the optical axis of a lens coincides with the geometric axis of the lens circumference or its barrel. Corresponding measurements are usually performed using distance sensors. In this proven approach, the autocollimator checks the centering of the optics and the distance sensors measure the position of the lens edge or the barrel. The combination of both partial results allows an assessment of the lens centering in relation to the edge. If the surface of the lens or barrel is sensitive or interrupted by segments (holes, cutouts, etc.), the use of non-contact distance sensors is advantageous.
The motorization
In addition to the proven manual solution, the OptiCentric® 101 now also allows the positioning of the respective sensor via a motor-controlled tool stage. This enables the sensor head to be brought into its measuring position with high absolute accuracy for horizontal (x) and vertical (z) directions as well as with regard to the tilt angle (theta). The theta motorization tilts the sensor and brings it into the correct tilt angle towards the barrel or lens surface. While distance measurement for mounts typically is horizontal and vertical, for aspheres a variable tilt is set that positions the sensor normal to the surface. This motorization allows switching between different lens and barrel types thus it is completed much faster after initial setup. The user-independent positioning ensures an overall higher process reliability.
Asphere measurement with AspheroCheck®
The alignment of the aspherical lens surface in regard to the paraxial optical axis is an important quality criterion for aspherical lenses – both axes must coincide. A corresponding check of the individual elements can be performed with the OptiCentric® AspheroCheck®: While an autocollimator measures the centering of the paraxial optical axis during a sample rotation, a distance sensor measures the run-out at an off-axis zone of the aspherical surface. In this way, precise information about the orientation of the aspherical surface is obtained.
Centration measurement in regard to the lens edge and barrel
Many applications require that the optical axis of a lens coincides with the geometric axis of the lens circumference or its barrel. Corresponding measurements are usually performed using distance sensors. In this proven approach, the autocollimator checks the centering of the optics and the distance sensors measure the position of the lens edge or the barrel. The combination of both partial results allows an assessment of the lens centering in relation to the edge. If the surface of the lens or barrel is sensitive or interrupted by segments (holes, cutouts, etc.), the use of non-contact distance sensors is advantageous.
The motorization
In addition to the proven manual solution, the OptiCentric® 101 now also allows the positioning of the respective sensor via a motor-controlled tool stage. This enables the sensor head to be brought into its measuring position with high absolute accuracy for horizontal (x) and vertical (z) directions as well as with regard to the tilt angle (theta). The theta motorization tilts the sensor and brings it into the correct tilt angle towards the barrel or lens surface. While distance measurement for mounts typically is horizontal and vertical, for aspheres a variable tilt is set that positions the sensor normal to the surface. This motorization allows switching between different lens and barrel types thus it is completed much faster after initial setup. The user-independent positioning ensures an overall higher process reliability.